Revealing the Intricacies of Fasteners and Machining Procedures for Optimal Performance
In the realm of engineering and manufacturing, the choice of bolts and the details of machining procedures play a pivotal role in establishing the utmost efficiency and resilience of a product. From the relatively simple job of choosing the ideal sort of bolt to the facility precision machining techniques utilized, every step in this process needs meticulous attention to detail. As we begin on this expedition right into the world of fasteners and machining, we will uncover the subtle yet important elements that can considerably affect the efficiency and quality of the end product, dropping light on the usually forgotten facets that can make all the distinction in accomplishing optimal efficiency.
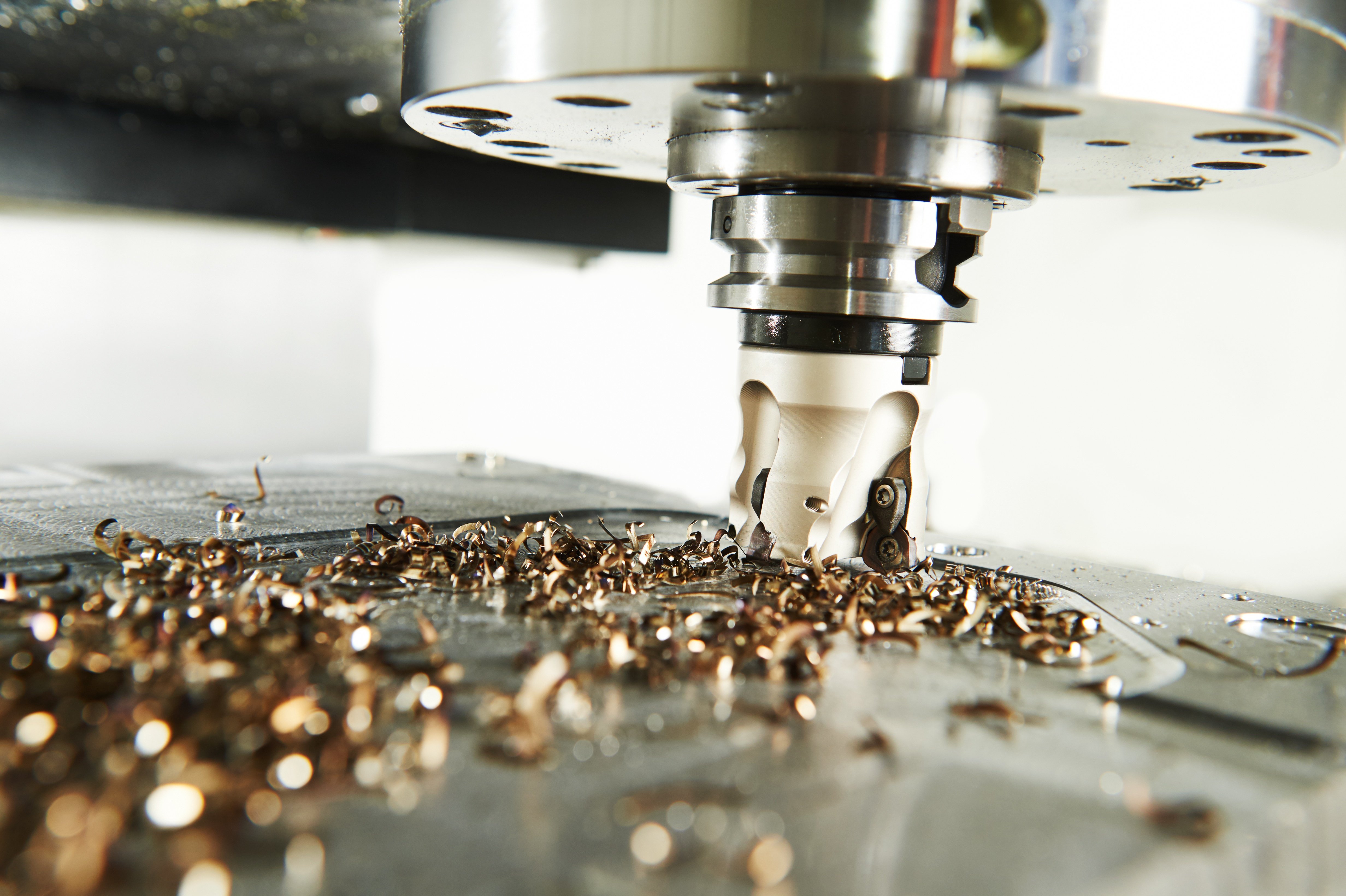
Importance of Proper Bolt Option
Selecting the ideal bolts is essential in making sure the architectural honesty and durability of any type of mechanical assembly. Fasteners play an essential role in holding parts with each other securely, with the right selection contributing substantially to the total performance and dependability of the setting up. When choosing bolts, factors such as material compatibility, environmental conditions, load-bearing capacity, and ease of setup should be carefully considered to guarantee ideal performance.
Improper fastener choice can cause a series of problems, including helping to loosen, deterioration, and even structural failing. Making use of fasteners that are not fit to the details needs of the assembly can compromise its performance and position safety risks. Designers and engineers must diligently examine the application needs and pick fasteners that meet or go beyond the necessary standards and requirements.
In addition, the proper fastener selection procedure involves analyzing the joint design, expected tons, vibration degrees, and potential thermal growth or contraction to ensure that the picked fasteners can hold up against the operating conditions properly. By prioritizing correct fastener option, makers can improve the quality, resilience, and efficiency of their mechanical assemblies.
Kinds and Characteristics of Bolts
A crucial facet of mechanical assemblies lies in comprehending the diverse kinds and special attributes of fasteners made use of in different industrial applications. Bolts are important components that hold structures together, making certain stability and functionality.
Screws are threaded bolts that are frequently used to sign up with two or even more elements with each other. Bolts are similar to screws yet are normally used with a nut to develop a secure joint. Nuts are inside threaded fasteners that mate with screws to hold components with each other. Washing machines are thin plates that disperse the tons of a bolt, avoiding damages to the material being attached. Rivets are permanent bolts that are hammered or pressed into area. Pins are utilized for placement or to protect parts temporarily.
Understanding the characteristics of each type of bolt is crucial for picking the ideal one for a specific application, making sure ideal performance and reliability of the mechanical setting up. Fasteners and Machining.
Accuracy Machining Methods for Effectiveness
The elaborate design needs of numerous bolts necessitate employing accuracy machining methods for optimal efficiency in making procedures. Precision machining is crucial in making certain that bolts meet the specific requirements needed for their intended application. Among the primary strategies utilized in precision machining is Computer system Numerical Control (CNC) machining, which allows high levels of precision and repeatability in the production of fasteners. CNC equipments are capable of performing intricate cuts and shaping procedures with minimal human intervention, leading to raised effectiveness and uniformity in the manufacturing procedure.
In addition to CNC machining, various other precision strategies such as grinding, milling, and turning are generally used to accomplish the limited tolerances needed for bolts. These techniques allow producers to develop fasteners with smooth surfaces, specific dimensions, and high structural stability. By making try this web-site use of precision machining methods, suppliers can enhance the high quality of fasteners, minimize product waste, and boost overall production effectiveness. The use of advanced machining processes assists make sure that bolts fulfill sector criteria and consumer assumptions for efficiency and dependability.
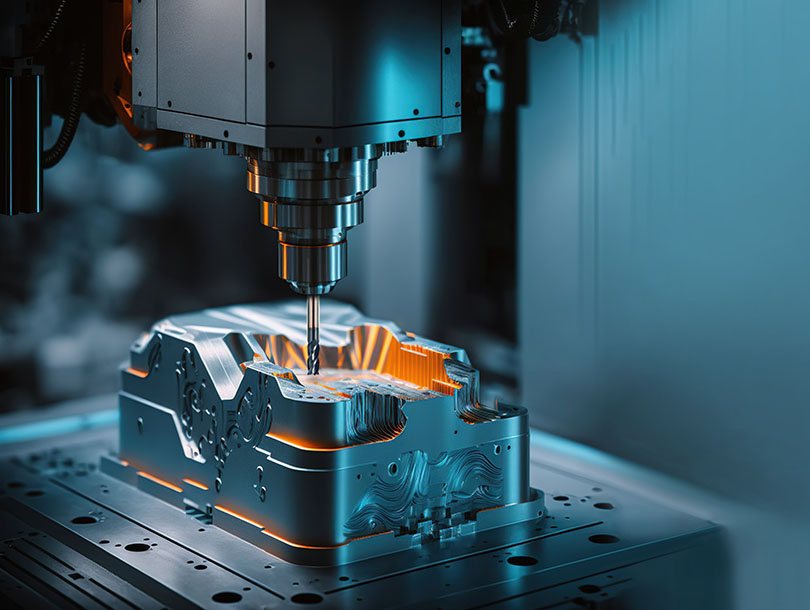
Variables Influencing Machining Refine Efficiency
Various variables play a substantial role in identifying the performance of machining processes in the production of fasteners. Optimizing these parameters based on the certain demands of the bolt being created is crucial to accomplishing economical and precise machining.
Device rigidness and stability likewise play an important function in figuring out machining procedure efficiency. A secure machine with minimal resonances can enhance precision and avoid device wear, leading to better overall efficiency. The skill and experience of the equipment driver can not be underestimated. A well-informed driver can make real-time changes, troubleshoot concerns successfully, and make sure that the machining process runs smoothly, eventually impacting the final high quality of the fastener.
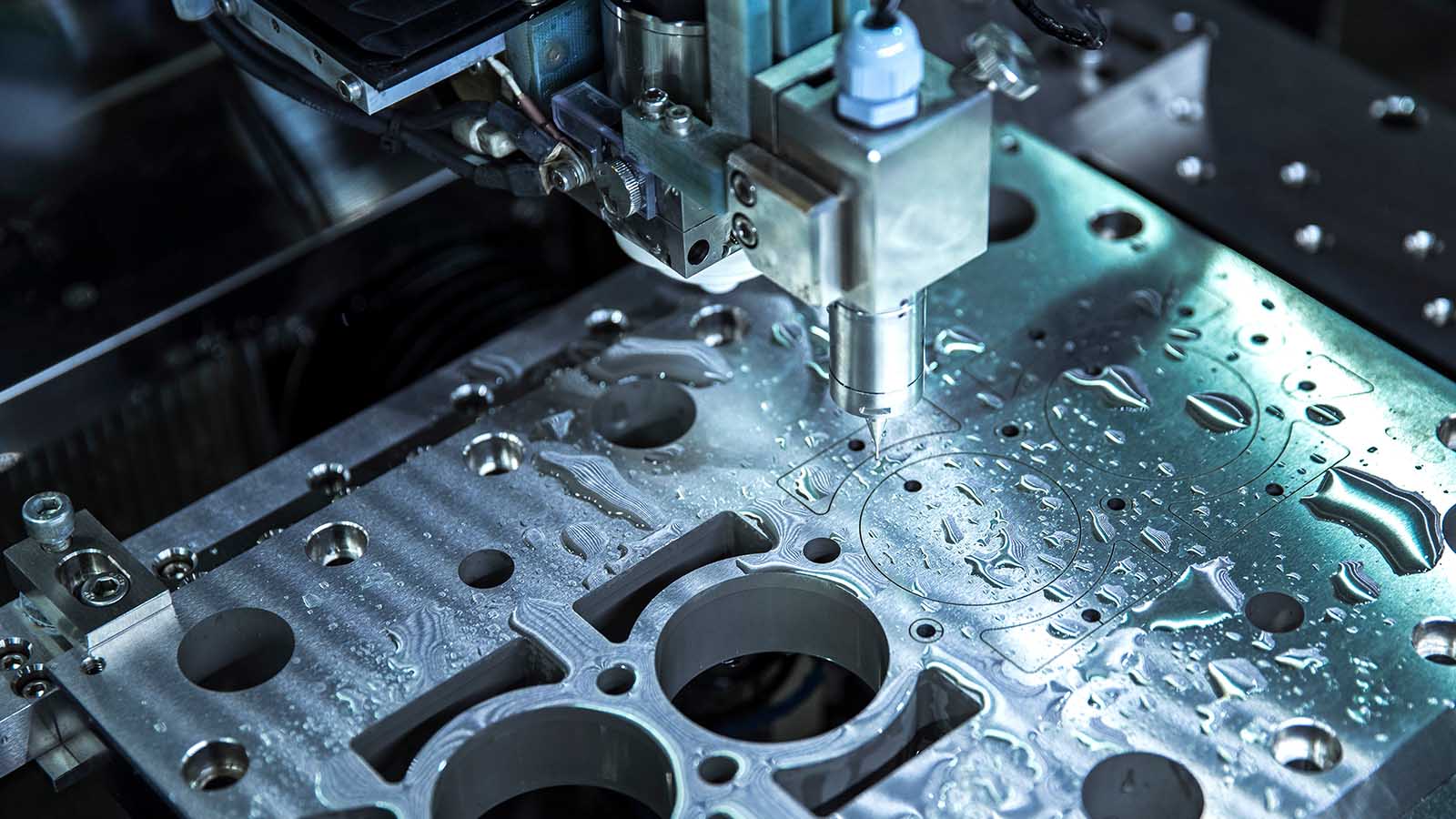
Quality Assurance Measures in Production
Variables influencing machining process performance, such as reducing device selection and device security, straight impact the application of i was reading this high quality control actions in manufacturing. Regular upkeep of machining equipment is additionally crucial to support high quality control. By sticking to stringent quality control procedures, producers can improve client complete satisfaction, develop a credibility for reliability, and eventually achieve optimal performance in their machining processes.
Conclusion
To conclude, choosing the best fasteners and using accuracy machining techniques are vital for optimum efficiency in producing procedures. Recognizing the kinds and characteristics of fasteners, along with aspects affecting machining process performance, can result in improved efficiency and quality assurance measures. By taking note of these intricacies, manufacturers can achieve greater degrees of performance and reliability in their products.
In the realm of engineering and production, the option of fasteners and the complexities of machining processes play a crucial duty in figuring out the supreme performance and durability of a product (Fasteners and Machining). One of the main strategies used in accuracy machining is Computer system Numerical Control (CNC) machining, which enables high degrees of precision and repeatability in the production of bolts. look at more info The use of advanced machining processes helps make sure that fasteners fulfill market standards and consumer assumptions for efficiency and reliability
In verdict, choosing the ideal bolts and utilizing precision machining techniques are crucial for ideal efficiency in producing procedures. Understanding the kinds and characteristics of bolts, along with elements affecting machining process efficiency, can lead to boosted effectiveness and top quality control steps.